Auszug aus dem ElektroModell 2/2001, von Ludwig Retzbach
Die Sache mit dem "Timing"
Bei Gleichstromelektromotoren ist immer wieder von "Timing" die Rede. Bei der modernen bürsten- und sensorlosen Motortechnik taucht der Begriff hingegen im Zusammenhang mit dem Controller auf. Was hat es damit auf sich?
Klar, Timing kommt von "time". Bei den RC-Car-Fahrern dient Timing dazu, die Rundenzeiten auf die vorhandene Batteriekapazität bzw. Akkuspannung (fein-) abzustimmen. Bei einem ideal getimten Auto reicht der "Saft" exakt bis zum Überfahren der Ziellinie. Timing beeinflusst also den Stromverbrauch und damit letztlich auch die Motorleistung. Dies geschieht durch Verdrehen des Bürstenträgers entgegen der Laufrichtung und hat einen positiven Nebeneffekt: Richtig dosiert, kompensiert das Timing die sog. Ankerrückwirkung, jene durch den Ankerstrom verursachte Verdrehung des magnetischen Feldes. Der Kommutierungszeitpunkt wird damit nach vorne korrigiert. Somit funkt es weniger und der Kollektorverschleiß wird reduziert. Der Winkel, um den das hintere Lagerschild gegen die Laufrichtung verdreht werden muss, hängt vom verursachenden Ankerstrom ab und kann daher bei herkömmlichen Motoren nur "über den Daumen" eingestellt werden, da sich der Strom ja ständig ändert.
Im Allgemeinen wird diese Vorkommutierung sogar etwas übertrieben und kommt damit einer Art "Frühzündung" gleich. Das heißt, die einzelnen Spulen werden etwas früher ein- und ausgeschaltet, als dies ihrem geometrischen Drehwinkel entspricht. Und selbst dies macht Sinn, weil Motorspulen letztlich Induktivitäten darstellen, bei denen der Strom nicht unmittelbar an die anliegende Spannung gekettet ist, sondern verzögert einsetzt und dafür beim Abschalten noch nachfließt.
Äußerlich erkennbarer Effekt einer überzogenen "Frühzündung" ist die Erhöhung des Motorstroms. Doch während sonst die Stromzunahme bei Elektromotoren stets dem Drehmoment zugute kommt, bewirkt sie hier einen Drehzahlanstieg. Wie kann das sein?
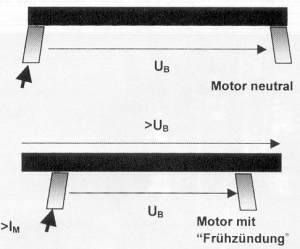
Ein stark vorgetimter Motor wirkt wie ein Transformator mit nur einer Wicklung, die zwei Anzapfungen trägt. Diese wandern mit zunehmender "Frühzündung" immer mehr nach innen. Dadurch wird die an den Kohlen anliegende Spannung Ub nur noch an einen Teil der Wicklung gelegt. Bezogen auf die Gesamtwicklung kommt dies einer Hochtransformation der Betriebsspannung gleich. Dies ist der Grund für die Drehzahlzunahme. Nach dem Energieerhaltungssatz muss daher auch der Motorstrom IM ansteigen.
Und beim Brushless ...?
Bürsten- und sensorlose Motoren sind zweifach im Vorteil: Die (die Kommutierung beeinflussende) Induktionsspannung folgt zumindest teilweise der Feldverschiebung; erledigt sich somit zu einem gewissen Teil automatisch. Zudem lässt sich der exakte Zeitpunkt nun nicht nur einmalig einstellen, sondern kontinuierlich während des Betriebs nachführen. Als beeinflussende Größen gelten primär der Motorstrom und die Drehzahl. Doch gerade mit der internen (Puls-)Strommessung hat der Großteil der Entwickler so seine liebe Not.
Diesen sich ständig verändernden Stromwert mit geeigneten Mitteln aufzuspüren und sekundenbruchteilgenau in eine exakt definierte Regelgröße umzusetzen, na ja, daran wird bei den meisten Herstellern noch gearbeitet. Und wer das Problem schlussendlich gelöst zu haben glaubt, wird es vielleicht lieber erst seinem Frisör denn einem Modell-Redakteur erzählen.
Viele Controller arbeiten mit einem nach wie vor fest eingestellten, oft ziemlich frühen Timing. Werte von ca. 30° gelten als beliebt, weil sich dann das Timing schön an die vorausgehende Phase anhängen lässt. Diese Motoren langen beim Strom ordentlich zu, bringen ein sattes Plus an Drehzahl und verschenken damit zwangsläufig wertvolles Drehmoment, was letztlich - vor allem im getakteten Betrieb -auch einige Prozentpunkte Wirkungsgrad kostet.
Daher gehen die Ingenieure mehr und mehr dazu über, die imaginären Bürstenträger verdrehbar, das Timing also wieder variabel zu gestalten. Auch werden den Strom indirekt beeinflussende Größen wie die Kanalimpulslänge (=Stellung des "Gas"-Knüppels) zur Variation des "Zündzeitpunkts" herangezogen.
Wie sich ein etwas zurückgenommenes Timing auswirkt, sei an hand des Lehner-Controllers LMT 3060 demonstriert, bei dem der Kunde das Timing selbst über eine PC-Schnittstelle verändern kann. Der Beispielmotor wurde bei einer Motorspannung von 18 V betrieben. Gemessen wurde der interessante Strom bereich von 15 bis 45 A.
Angaben ohne Gewähr